July 17th, 2024
Optimize your Design for Manufacturability in 7 Steps
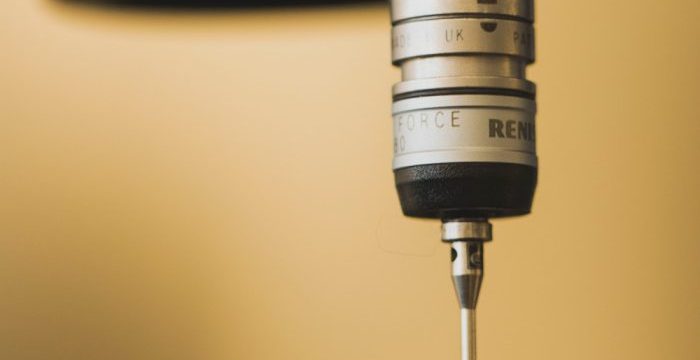
Optimize your Design for Manufacturability in 7 Steps
Transitioning a design from R&D to production can be daunting. At CITO Medical, we simplify this process by ensuring your product is optimized for efficient, cost-effective manufacturing. The following seven steps will guide you in designing for manufacturability, helping you achieve a seamless transition to production:
1. Simplify the Design
- Reduce Part Count: Minimize the number of parts in the assembly to streamline inspections, shorten assembly time, and decrease overall complexity.
- Standardize Components: Utilize off-the-shelf components whenever possible. For smaller production runs, these are often more cost-effective than custom parts.
- Design for Modularity: Incorporate subassembly modules to streamline assembly, testing, and manufacturing processes.
2. Material Selection
- Choose Common Materials: Opt for materials that are readily available to reduce costs and lead times.
- Leverage Established Processes: Select mature manufacturing processes that are well-suited to the materials you’ve chosen.
3. Assembly Considerations
- Ease of Assembly: Integrate features into your design that simplify the assembly process and ensure consistency across your product line.
- Minimize Fasteners: Reduce the number of fasteners by using snap fits, press fits, or other alternatives to screws and adhesives where possible.
- Ensure Accessibility: Design with the necessary tools in mind, considering ergonomics and ease of use during assembly.
4. Manufacturing Processes
- Select Appropriate Methods: Choose manufacturing processes that align with your design’s requirements.
- Consider Tolerances: Specify tolerances that are realistic for the chosen manufacturing methods. Avoid overly tight tolerances that can drive up costs.
- Facilitate Testing & Quality Control: Design parts to be easily testable and inspectable throughout the manufacturing process.
5. Cost Considerations
- Optimize Production Time: Reduce labor costs by minimizing machining steps and simplifying assembly processes.
- Design for Automation: Consider automating parts of your manufacturing process. Even small fixtures can reduce labor costs and increase consistency—your quality control team will thank you!
- Cut Molding Costs: For injection-molded parts, consider upgrading to multi-cavity tooling to reduce per-part costs.
6. Supplier Selection
- Engage Early: Involve manufacturing engineers early in the design process to gain valuable insights and preempt potential issues.
- Vet Suppliers Thoroughly: Evaluate new suppliers by inspecting multiple lots of the same part, and always have secondary sources for critical components.
7. Documentation and Communication
- Clear Documentation: Provide detailed drawings, specifications, and assembly instructions to clearly communicate design intent to the manufacturing team.
- Continuous Feedback: Foster a culture of continuous improvement by establishing feedback loops between your manufacturing and engineering teams.
At CITO Medical, we prioritize manufacturability from the very start. By integrating these principles throughout the product lifecycle—from initial brainstorming to early prototyping—we help you avoid costly redesigns and keep your project on track. Contact us today to see how we can support your next development project.
Other Posts
Stay in Touch
Sign up for updates about our latest projects and innovations.